Galvanized coating layer also forms a protective film on the surface. This protective film, however, is not as fine as in ZAM™, and less adhesive (see photo at right).
In contrast, the protective film formed on the coating surface of ZAM™ is excellent in both fineness and adhesion, and consequently it inhibits permeation of corrosion factors, preserving high corrosion resistance over a long period.
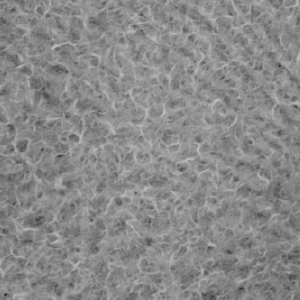
ZAM™
2㎛
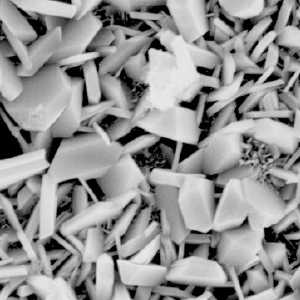